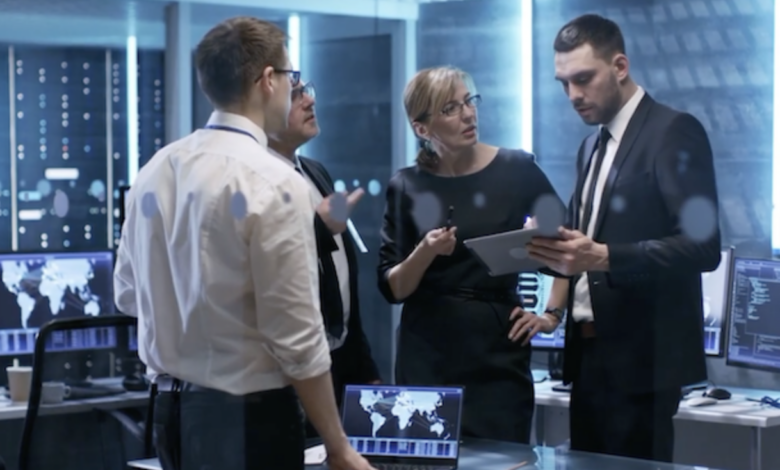
In the rapidly changing landscape of industrial technology, artificial intelligence (AI), and advanced analytics have emerged as transformative forces, particularly in the manufacturing sector. As companies seek to optimize operations at all levels, improve efficiencies, and maintain a competitive edge, AI-driven platforms are becoming imperative for addressing complex business challenges in manufacturing processes.
Industrial AI and analytics combine AI algorithms, machine learning models, and advanced analytics tools to extract actionable insights from tremendous amounts of industrial data. This powerful combination empowers organizations to make informed decisions, boost operational efficiency, predict maintenance needs, and improve sustainability and safety standards in a very demanding sector. Surprisingly, the potential of industrial data remains largely untapped, with less than 20% of data generated by industrial companies being utilized effectively.
Why? Significant challenges can be found in today’s industrial landscape, such as:
- Quality Variability: Fluctuations in raw material properties or process conditions can result in inconsistent product quality.
- Data Silos: Manufacturing data is often spread across multiple systems, making holistic analysis difficult, resulting in data silos.
- Manual Workflows: Traditional approaches to monitoring and reporting often involve time-consuming and error-prone manual processes.
- Regulatory Compliance: Many industries must meet stringent regulatory requirements, necessitating detailed reporting and traceability for compliance.
- Operational Inefficiencies: Unoptimized production parameters, extended cycle times, and frequent changeovers can increase costs and reduce throughput, leading to operational inefficiencies.
- Skills Gap: Many organizations face a shortage of skilled professionals who can effectively implement and manage AI systems in industrial settings, creating a skills gap.
By analyzing data collected from equipment, AI models can forecast upcoming issues, enabling proactive management of machines and hardware. This optimal approach minimizes downtime, extends equipment lifespan, and reduces maintenance costs, ultimately leading to significant improvements in operational efficiency.
AI-driven quality control systems can analyze real-time data to identify potential issues before they occur. This includes the use of “golden batch” profiles, which represent ideal operating conditions based on historical data from successful batches. Deviations from these profiles can be flagged in real-time, allowing operators to take corrective action promptly – a perfect example of Human-AI Teaming (HAIT).
Advanced AI systems excel at identifying abnormal events and outliers in industrial data. By analyzing data from machines, sensors, and industrial operations, these systems can detect aberrations that might otherwise go unnoticed, allowing for better process control and optimization – critical to the manufacturing industry.
AI-powered analytics tools can also automate report generation by consolidating data into customizable templates that meet industry standards. This reduces administrative workload while ensuring accuracy and traceability for regulatory compliance.
The adoption of these technologies offers several tangible benefits, including:
- Improved Product Quality: Early deviation detection ensures consistent product quality across batches and production runs, which is essential in manufacturing.
- Enhanced Efficiency: Automation reduces reliance on manual workflows for tasks like data collection, analysis, and reporting, improving efficiency.
- Cost Savings: Optimized processes minimize waste, rework, and downtime while improving resource utilization, allowing for a competitive edge.
- Regulatory Compliance: Automated reporting ensures manufacturers meet industry standards without additional administrative burden, optimizing workflows.
- Informed Decision-Making: Real-time insights enable operators to make data-driven decisions quickly, improving overall agility, aiding in improved performance.
To maximize the benefits of AI and advanced analytics in manufacturing, organizations should consider the following best practices outlined below:
- Develop a Clear Strategy: Create a comprehensive and clear industrial operation strategy that incorporates AI, knowledge management, and value chain integration.
- Focus on Specific Use Cases: Start with well-defined, high-value use cases to demonstrate potential and build momentum for wider adoption.
- Ensure Data Integration and Quality: Consolidate historical and real-time data from various sources into a unified platform, ensuring data quality and compatibility.
- Invest in Training and Upskilling: Prioritize the development of AI skills within the organization to ensure effective implementation and management of AI systems, including training and corporate culture assurances that position AI as “helper” and not a “replacer.”
- Foster Cross-Industry Collaboration: Share lessons learned and best practices across industries to accelerate the scaling of AI initiatives. Open lines of communication – both internally and externally – promote goodwill and build strategic relationships across the sector.
- Iterate for Continuous Improvement: Use insights gained from analytics tools to refine processes over time, continuously optimizing manufacturing operations for best results.
Conclusion
As industrial sectors continue to embrace AI and advanced analytics, the focus remains on balancing technological advancement with human expertise. The concept of HAIT should be a gold standard for every organization leveraging AI. By prioritizing strategic implementation, workforce development, and cross-functional collaboration, as well as upskilling and corporate culture initiatives, companies can harness the full potential of these technologies to drive innovation, efficiency, and competitive advantage in the evolving landscape of industrial operations.