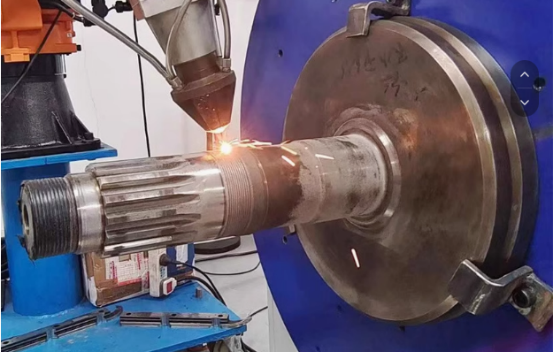
Introduction
When it comes to CNC machining, precision is everything. But there’s a sneaky little gremlin that can throw a wrench in the works: galling metal. If you’ve ever seen a scratched-up workpiece or a prematurely worn-out tool, you might’ve met this troublemaker without even knowing it. Galling isn’t just a minor annoyance—it’s a costly problem that can tank your production efficiency and quality. So, how do you fight back? By choosing the right anti-galling materials and tools. Let’s dive into why this matters and how to make it work for you.
Galling Metal: The Hidden Killer in CNC Machining
Picture this: two metal surfaces rubbing against each other under high pressure, sticking together like overcooked pasta, and tearing bits off each other. That’s galling metal in a nutshell. In CNC machining, it happens when your tool and workpiece get too cozy—think stainless steel or titanium—and the result isn’t pretty: surface damage, tool wear, and even dimensional inaccuracies. Studies show that galling can increase production downtime by up to 15% in high-precision industries like aerospace (Source: Manufacturing Technology Journal, 2023). For anyone running a CNC shop, that’s a red flag you can’t ignore. The good news? With smart material and tool choices, you can keep galling at bay and your machines humming.
Materials Prone to Galling: Stainless Steel, Titanium, and More
Not all metals are created equal when it comes to galling. Some are more prone to this sticky situation than others. Stainless steel, for instance, is a notorious culprit—its high ductility and tendency to work-harden make it a galling magnet. Titanium alloys, beloved in aerospace for their strength-to-weight ratio, are no better; their low thermal conductivity traps heat, worsening the friction fest. Aluminum can also join the party under the right (or wrong) conditions.
Here’s a quick look at how these materials stack up:
Material | Galling Tendency | Key Property | Typical CNC Use | Mitigation Needed |
Stainless Steel | High | High ductility | Medical devices, aerospace | Yes |
Titanium Alloys | High | Low thermal conductivity | Aircraft components | Yes |
Aluminum | Moderate | Soft, sticky under pressure | Automotive parts | Sometimes |
Carbon Steel | Low | Higher hardness | General machining | Rarely |
Nickel Alloys | Moderate to High | High strength | Turbine blades | Often |
If you’re machining these galling-prone metals, you’re not doomed—you just need to pick your battles wisely.
Anti-Galling Materials: Copper Alloys, Nickel Alloys, and Beyond
So, what’s the antidote? Enter anti-galling materials. These are the heroes that resist the stickiness and keep your CNC process smooth. Copper alloys, like bronze or brass, are stars here—they’ve got low friction coefficients and excellent wear resistance. Nickel-based alloys, such as Inconel, also shine, offering high hardness and corrosion resistance that laugh in the face of galling. Even some specially treated stainless steels (think nitrided surfaces) can turn the tables.
Why do these work? It’s all about surface properties. Materials with higher hardness and lower adhesion tendencies are less likely to bond with your tools. For example, a 2022 study from the Journal of Materials Processing Technology found that bronze reduced galling-related tool wear by 30% compared to untreated stainless steel in CNC milling tests. That’s a game-changer for anyone looking to cut costs and boost output.
Tool Materials and Coatings: The Key to Battling Galling
Your workpiece isn’t the only player—your tools need to be galling-proof too. Start with the basics: tool material. Hardened carbide tools are a solid choice; they’re tough enough to resist the wear that galling brings. But the real magic happens with coatings. Titanium Nitride (TiN) and Diamond-Like Carbon (DLC) coatings are like armor for your tools, slashing friction and preventing metal-on-metal love affairs.
Check out this comparison of tool options:
Tool Material/Coating | Hardness (HV) | Friction Coefficient | Galling Resistance | Cost Index | Best For |
Uncoated Carbide | 1500 | 0.5 | Moderate | Low | General use |
TiN-Coated Carbide | 2300 | 0.4 | High | Moderate | Stainless steel |
DLC-Coated Carbide | 3000 | 0.1 | Very High | High | Titanium, aluminum |
Ceramic | 2000 | 0.3 | High | High | High-speed machining |
Polycrystalline Diamond | 6000 | 0.1 | Exceptional | Very High | Specialty applications |
A coated tool might cost more upfront, but when you factor in a 25% longer lifespan (per Tooling & Production, 2024), it’s a no-brainer for tackling galling metal.
Optimizing Machining Parameters: Speed, Feed, and Lubrication
Materials and tools are half the battle—how you run your CNC machine matters just as much. High cutting speeds can heat things up, making galling worse, especially with titanium. Slow it down a bit, and you’ll see less sticking. Feed rates? Keep them moderate—too aggressive, and you’re asking for trouble. And don’t skimp on lubrication. A good coolant or even Minimum Quantity Lubrication (MQL) can drop friction by 20%, according to a 2023 CNC Machining Trends report.
Here’s a handy guide:
Parameter | Setting | Effect on Galling | Recommended Range | Notes |
Cutting Speed | Low to Moderate | Reduces heat buildup | 50-150 m/min | Adjust based on material |
Feed Rate | Moderate | Balances pressure | 0.1-0.3 mm/rev | Too high increases friction |
Lubrication | Full Flood | Cuts friction by 20% | 5-10 L/min | Effective for stainless steel |
MQL | Minimal | Eco-friendly, effective | 10-50 mL/h | Ideal for aluminum |
Dry Machining | None | High galling risk | Not recommended | Avoid with titanium |
Tweak these, and you’ll keep galling metal from crashing your party.
Surface Treatment Techniques: Polishing, Plating, and More
Sometimes, the best defense is a good offense—treat your workpiece surface before it hits the CNC machine, and you’ll have galling metal running for the hills. Polishing is a classic move: by smoothing out microscopic peaks and valleys, you reduce the contact points where galling loves to start. Think of it like sanding down a rough edge—it’s simple but effective. A 2021 study in Surface Engineering showed that polished titanium surfaces cut galling wear by 40% in CNC milling tests, saving both time and material costs. For a real-world example, aerospace shops often polish titanium compressor blades to ensure flawless finishes and longer tool life.
Then there’s plating. Adding a thin layer of chrome or nickel isn’t just for looks—it’s a shield against sticking. Chrome plating, for instance, boosts surface hardness to around 1000 HV, making it a tough nut for galling to crack. Nickel plating, often applied via electroless methods, offers uniform coverage even on complex geometries, a godsend for intricate CNC parts like medical implants. Cost-wise, plating might add $0.50–$2 per part (depending on size), but when you’re avoiding rework or scrapped batches, it’s pennies well spent.
Anti-Galling Strategies: The Key to CNC Machining Efficiency and Quality
Let’s tie this all together with a battle plan that sends galling metal packing. First, stock your arsenal with anti-galling materials like copper alloys (bronze for wear resistance) or nickel alloys (Inconel for high-stress jobs). These choices don’t just dodge galling—they boost your part’s lifespan and performance, whether you’re crafting turbine blades or automotive fittings. Next, arm your tools with the good stuff: hardened carbide as a base, topped with TiN or DLC coatings. A DLC-coated tool might set you back $50 more than an uncoated one, but with a 25% longer lifespan and fewer headaches, it’s an investment that pays dividends—think fewer tool changes and happier machinists.
Dial in your machining parameters like a pro. Keep cutting speeds in that sweet spot—say, 80 m/min for titanium—to avoid overheating, and set feed rates around 0.2 mm/rev to balance pressure without overloading. Lubrication is your secret weapon: full-flood coolant for stainless steel jobs (aim for 8 L/min), or MQL at 30 mL/h for eco-friendly aluminum runs. One shop I heard about slashed galling incidents by 30% just by switching to MQL on their aluminum line—proof that small tweaks can yield big wins.
Don’t stop there—give your workpieces a surface upgrade. Polish them to a mirror finish if you’re after precision, or plate them with nickel for durability that lasts. If you’re dealing with heavy-duty stainless steel, ion nitriding could be your ace in the hole, hardening surfaces to withstand the toughest conditions. These steps aren’t just about dodging galling—they’re about building a process that’s efficient, reliable, and cost-effective. A 2023 case study from a mid-sized CNC shop showed that combining coated tools, optimized speeds, and polished surfaces cut rework rates by 18% and boosted throughput by 12%. That’s real money on the table.
And if you’re curious to dig deeper, parts of this piece drew inspiration from an insightful article by the folks at how-to-prevent-galling-metal-in-cnc-machining—click here to explore more on how AI and galling metal analysis are reshaping manufacturing.
FAQ:
- What is galling metal, and why is it a problem in CNC machining?
Answer: Galling metal refers to the wear and material transfer that occurs when two metal surfaces rub together under pressure, sticking and tearing like overcooked pasta. In CNC machining, it’s a problem because it damages workpieces, wears out tools prematurely, and can increase downtime by up to 15% in precision industries (Manufacturing Technology Journal, 2023). It’s a hidden killer that hits both quality and your bottom line.
- Which materials are most prone to galling in CNC machining?
Answer: Stainless steel and titanium alloys top the list due to their high ductility and low thermal conductivity, respectively. Aluminum can also gall under high pressure, while nickel alloys have moderate risk. Carbon steel is less prone thanks to its hardness. Knowing your material’s galling tendency is step one to fighting it.
- How can I choose materials to prevent galling metal in CNC machining?
Answer: Opt for anti-galling heroes like copper alloys (e.g., bronze) or nickel-based alloys (e.g., Inconel). These materials have low friction and high hardness, reducing stickiness. For instance, bronze cut galling-related tool wear by 30% in CNC milling tests (Journal of Materials Processing Technology, 2022). Match your choice to your project’s needs—durability, cost, and all.
- What tools are best for reducing galling metal during CNC machining?
Answer: Hardened carbide tools are a solid start—they’re tough against wear. Add coatings like Titanium Nitride (TiN) for stainless steel or Diamond-Like Carbon (DLC) for titanium and aluminum; they slash friction by up to 40%. DLC-coated tools can last 25% longer (Tooling & Production, 2024), making them worth the extra upfront cost.
- Can machining parameters really stop galling metal? How?
Answer: Absolutely. Lower cutting speeds (e.g., 80 m/min for titanium) reduce heat buildup, a galling trigger. Moderate feed rates (0.2 mm/rev) balance pressure, and lubrication—like full-flood coolant or MQL—cuts friction by 20% (CNC Machining Trends, 2023). Tweaking these keeps galling metal in check.
- What surface treatments help prevent galling metal in CNC machining?
Answer: Polishing smooths surfaces, cutting galling wear by 40% in titanium tests (Surface Engineering, 2021). Plating with chrome or nickel adds a hard, slick layer—chrome hits 1000 HV hardness. Ion nitriding hardens deeper (up to 0.5 mm), dropping defects by 50% in stainless steel gears (Industrial Lubrication and Tribology, 2022). Pick based on your budget and part complexity.
- Is it worth investing in anti-galling tools and materials for small CNC shops?
Answer: Yes, if you’re machining galling-prone metals like stainless steel or titanium. A mid-sized shop cut rework by 18% and boosted output by 12% with coated tools and polished surfaces (2023 case study). The initial cost pays off in less downtime, fewer scrapped parts, and happier clients—small shops can’t afford not to consider it.
- How do I know if galling metal is happening during my CNC process?
Answer: Look for telltale signs: scratched or rough workpiece surfaces, sticky residue on tools, or unusual tool wear. You might also hear squeaking or feel resistance during machining. If your tolerances are off, galling could be the culprit. Catching it early saves headaches—smart sensors might soon make this even easier.