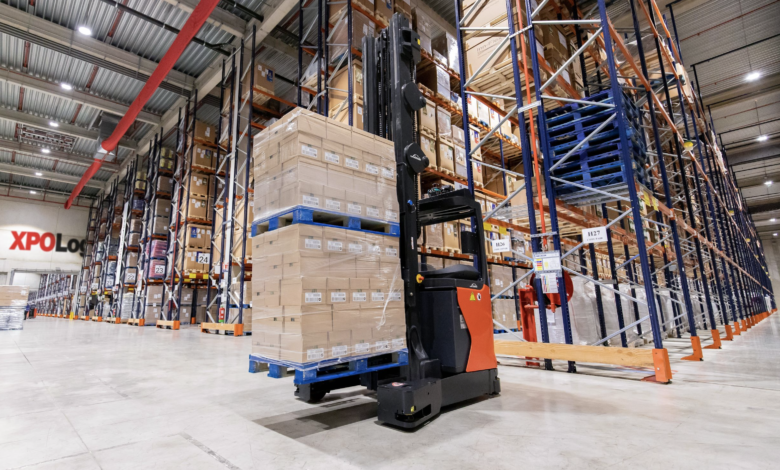
E-commerce has long represented both challenges and opportunities for e-tailers and omnichannel retailers. Now, a spotlight has been shown on both aspects of e-commerce by the acceleration of online shopping during the pandemic. Consumer expectations are rising along with e-commerce volumes, and success is being defined from the consumer’s perspective.
In the process, e-fulfilment and returns management have become complex undertakings that increasingly require the use of advanced automation. This is one of the foremost trends in logistics today — and, as logistics operations become more reliant on automation for satisfactory results, the combination of humans and machines that is driving efficiency can help improve health and safety as well.
The importance of physical well-being for distribution centre colleagues is well-documented in the industry and a priority for us at XPO Logistics. It’s encouraging to see the industry focus on sustainable remedies, because there is work to be done. In 2020, in Great Britain alone, the transportation and storage industry had an estimated 28,000 cases of workers who sustained non-fatal injuries. This includes slips, trips and strains, according to The Health and Safety Executive (HSE) Report.
Logistics businesses can benefit from adopting global best practices for health and safety. Our comprehensive safety strategy at XPO starts with instilling safety awareness up front through colleague education and on-the-job reinforcement, managed with strong safety systems. We take the workplace design into account at each site, as well as the activities performed. Our goal is zero occupational accidents.
What makes our approach atypical in many cases is our investments in technology to make logistics operations more efficient and safe. Many of these deployments utilise machine learning and artificial intelligence (AI) in robotics and other advanced automation to help improve worker safety.
Large-scale automation within a distribution centre can minimise human exposure to tasks that carry physical risks. For example, in some warehouses with multiple storage levels, we use robotic cranes to retrieve stock from shelves that are difficult to reach. This reduces the probability that an employee will sustain an injury by having the robotic crane perform work at height.
While the connection between AI and worker safety is obvious when a robot handles a difficult task on its own, there are also applications that bring out the best in humans and robotics. We’ve had notable success in using collaborative robots — called cobots — in our warehouses to support our human colleagues.
Cobots are mobile robots that team up with distribution centre staff to help with daily operations. They excel at order fulfilment. Humans and their cobots typically navigate the distribution centre together, with the cobot guiding the way to shelves where stock can be ‘picked’ for orders and transported to packing stations. The cobots are super-organised — they use machine learning to manage the components of each order and ensure accuracy. In our experience, when cobots and their human team members work side by side, productivity rates double on average, with accuracy increasing by as much as 40%.
Like other forms of automation, the cobots also reduce physical strain on workers. They handle loads safely and efficiently, without the hesitation that can lead to human error. Cobots also use advances in onboard AI and sophisticated sensors to navigate around humans safely. Another area where cobots make a meaningful difference is by mitigating worker fatigue, which can trigger occupational safety incidents.
Almost all of the benefits of cobots tie in some manner to the machine learning software they use. For example, when a cobot learns how to eliminate unnecessary walking, it makes the order fulfilment process more efficient, and it also reduces the risk of human injury from congestion in the aisles. This is especially important when a distribution centre manages seasonal volume surges, requiring an influx of temporary workers. Because the cobots take care of new workers who are unfamiliar with the premises, they help the workers be productive and safe from day one.
In yet another implementation of cobot technology, the robot can be programmed to climb up storage shelves to pick the products and bring them back down to their human team member below. At some of our warehouses, cobots are trained to go off and find the necessary products on their own, allowing their human counterparts to be more productive with their time during fulfilment.
While industries like automotive manufacturing have pioneered certain cobot applications, the logistics industry will be a major consumer of this technology in the future — and the current benefits to safety and productivity will likely represent a small fraction of what can be achieved. It’s exciting to contemplate the wide-open future for machine learning and AI applications in logistics environments.
This doesn’t mean human workers will become obsolete. Instead, as intelligent automation takes on the more physically demanding aspects of logistics work, our industry will become increasingly more attractive to a wide demographic of human workers.