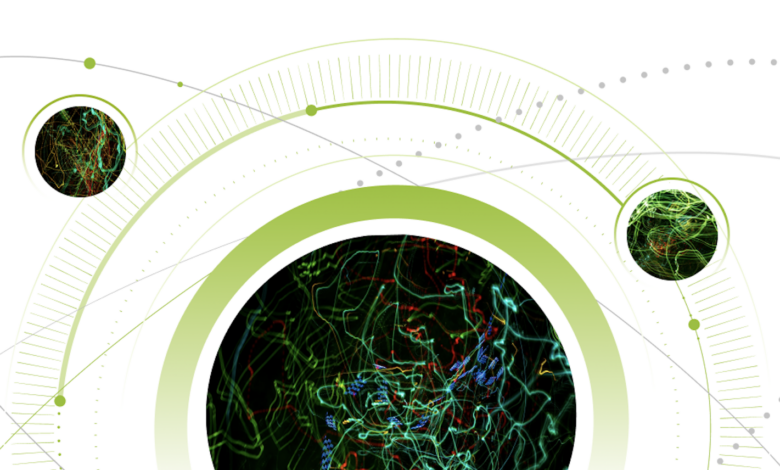
In recent years, the term “Digital Twin” has become an integral part of conversations about modern technology and innovation, covering many industries. This concept is a virtual model of a physical object, system, or production process that allows you to monitor, analyze and predict the behavior of the real counterpart in real time. Digital Twin manufacturing is not just a buzzword, it is one of the pillars of the new industrial revolution. Despite its growing popularity, Digital Twin technology has yet to penetrate many sectors of the economy, its potential looks promising.
Practical application of Digital Twins in the oil and gas industry
The trend towards the implementation of Digital Twins is particularly noticeable in key industries such as metals, mining, power generation, and oil and gas. These sectors are characterized by a continuous production cycle, which makes the use of the technology particularly useful.
Digital Twins are virtual models of physical objects, processes, or systems that allow companies to conduct detailed simulations of various scenarios. These models help not only in analyzing and optimizing current processes and planning, but also in predicting potential problems, which in turn makes it possible to identify potential risks in advance and find the best ways to address them.
Using Digital Twins, enterprises can conduct a comprehensive risk analysis by modeling various threats and “what-if” scenarios. This allows to identify the most vulnerable areas in the production chain, critical modes of operation and equipment parameters, as well as to develop effective measures to prevent abnormal situations. The application of Digital Twin in the oil and gas industry is almost limitless, every production process from exploration and production to refining can be improved using this technology. Digital Twin is a complex system that integrates data from various sources and utilizes advanced artificial intelligence and machine learning algorithms.
In exploration, Digital Twin can be used to create virtual replicas of fields that take into account geological features, reservoir properties, seismic data, etc. Thus, thanks to modeling different scenarios on the field twin, it is possible to test different variants of mineral extraction. For example, changing the drilling rig’s operating mode and assessing how effective it will be, or testing the impact of different oil recovery methods. Thanks to Digital Twins, oil and gas companies can assess the potential of a field, predict production volumes, and choose the optimal development strategy, minimizing the risks of drilling empty wells.
The “what if” Digital Twin scenario is applicable to drilling rigs as well. An oil and gas company is able to simulate drilling operations in real time and optimize the drilling process under changing conditions. What’s more, Digital Twins provide comprehensive equipment condition monitoring. They can predict the probability of equipment failures, optimize pump and compressor operating modes, monitor pipeline integrity and prevent leaks. Continuous data analysis and modeling allows identifying bottlenecks in the production process and taking timely measures to eliminate them.
Oil and gas is a potentially dangerous industry. Ensuring the safety of production facilities is one of the main goals for the development of the oil and gas industry. Digital Twins offer unprecedented opportunities to improve safety and efficiency. A digital replica accurately reflects the physical characteristics, operating processes and interrelationships of all components, and it is possible to simulate various critical scenarios on such a platform. For example, emergency response plans, including optimizing evacuation routes and firefighting equipment placement, can be developed in advance. Moreover, Digital Twins allow for virtual training of personnel. Employees can practice various scenarios in a safe environment, gaining the necessary experience without risk to life and health, as well as without significant financial costs.
In today’s realities, a fundamentally new approach to the digitalization of oil and gas production is emerging — the creation of ecosystems. The key aspect is the integration of Digital Twins into a single system. For example, virtual models of installations can be combined into one Digital Twin, which will display not only their individual characteristics, but also the interactions between them. In this way, it is possible to monitor the operating parameters of the entire site, identify bottlenecks and optimize the entire production process chain.
The challenges of implementing Digital Twins
Despite the popularity of Digital Twins of manufacturing processes, there are a number of significant challenges that can hinder the successful implementation of initiatives. One major challenge is the lack of data collection and limited storage capacity. When the amount of data is small or incomplete, it leads to additional errors in predictions, which in turn reduces the economic value of the twin. To develop an adequate and efficient model, it is necessary to collect all data that can influence the process, including target values. This requires not only technical solutions but also a strategic approach to data management.
Another significant difficulty associated with Digital Twin implementation is organizational measures. This is because the implementation of such innovative approaches is often perceived as a threat to the usual order of things. Workers in charge of operations at production sites may prefer to rely on their expertise, which can lead to resistance to change. To address this problem, reassigning some responsibility from employees to automated services will reduce stress levels and increase trust in new technologies. Despite these challenges, the adoption of Digital Twin technologies is becoming an integral part of today’s oil and gas industry. They can significantly reduce the cost of production, improve its quality and competitiveness in the market. Moreover, Digital Twins can help to optimize processes, improve planning and increase production flexibility.
Digital Twin — a tool to improve oil production efficiency
Digital Twin in the oil and gas industry is an integrated approach to asset management that can significantly improve the efficiency of all stages of production, reduce operating costs, minimize risks and ensure personnel safety. Further development of artificial intelligence and machine learning technologies promises even wider application of digital twins in oil and gas, opening up new opportunities for optimization and innovation in this industry.
Successful implementation of Digital Twins requires a comprehensive approach that includes both technical and organizational aspects. It is necessary to ensure quality data collection, create conditions for employee motivation and develop common goals for all production sites. Ultimately, the implementation of Digital Twins will not only improve internal processes, but also create new opportunities for oil and gas companies in a rapidly changing market and competitive environment.